The Advantages of Programmable Logic Controllers in Industrial Settings
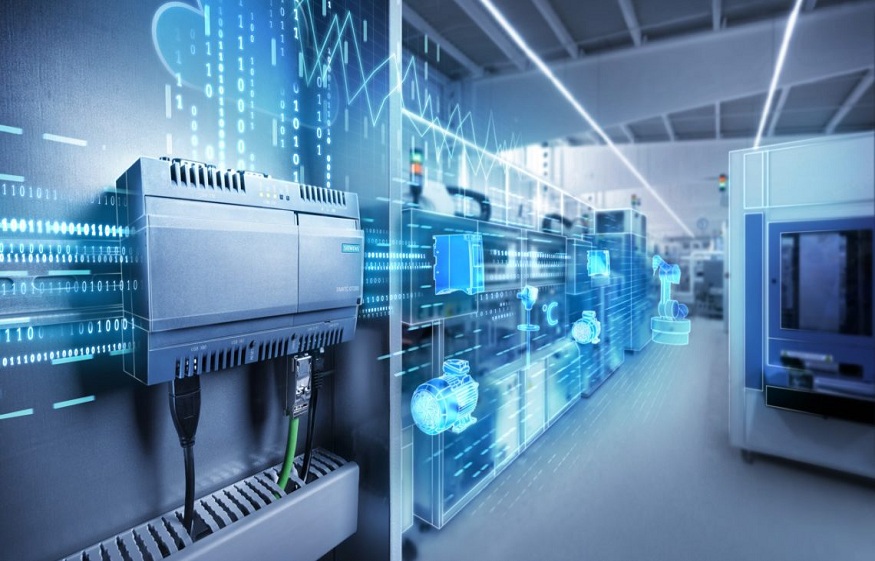
PLCs monitor the inputs and outputs of a machine and use artificial intelligence (AI) to make logic-based decisions for the machine or any other automated process. PLCs have sensors, sequencers, and internal timers that gather data from a machine. The data is analysed and used to deliver the output as per pre-set parameters.
Why are PLCs necessary in an industrial setting?
As mentioned earlier, these specialised computers can be used to control machinery and make decisions according to a set program. PLCs ensure higher productivity and are used in applications across numerous sectors, including automobile, chemical, manufacturing, glass, energy, engineering, HVAC, oil and gas industries. They are also used in day-to-day applications such as fire and burglar alarms, traffic control systems, lifts, automatic parking systems, automatic tank filling systems, and home automation.
Advantages of Programmable Logic Controllers in Industrial Settings
Glass Industry: PLCs have been widely used in various processes in the glass industry. For example, right from controlling the material ratio to processing of flat glasses, PLCs have played an important role in both digital quality control and position control. Integrating PLCs have not only enhanced the reliability and flexibility of the control system but also ensures that the output provided is of the best possible quality.
Manufacturing Industry: PLCs are used to regulate many parameters in the process of manufacturing cement and high strength steel. In cement plants, PLCs are used to provide the precise percentage of components during mixing processes to get the best possible quality. Additionally, PLCs are also used to control supporting tasks such as lab automation, hydraulic processes, etc.
In the steel manufacturing processes, PLCs are used to automate production processes which not only improves the quality of steel but also the production rate and accuracy in the production line, saving huge production costs.
Food and Beverage Industry: PLCs have faster internal timers, sequencers and relays which can ensure higher productivity. These advantages widely come into use in the food and beverage production lines.
All sequential and repeated operations in this industry are carried out using PLCs. For example, in the food and beverage industry, an element may need to be injected when the pressure or temperature reaches a very specific value. With PLCs integrated into the production lines, the speed, accuracy and efficiency of production have increased; operator costs and operation times have decreased, and hazards have been reduced.
Packaging industry: PLC control system is used in food packaging machinery. It can not only do the sealing but can also be used as an automatic beverage filling machine, bottling, labelling and packaging machine.
To browse through our high-quality programable logic controller and other industrial computing devices visit our website. There are several other types of PLCs from mounting to programming interfaces to programming languages, and network types.